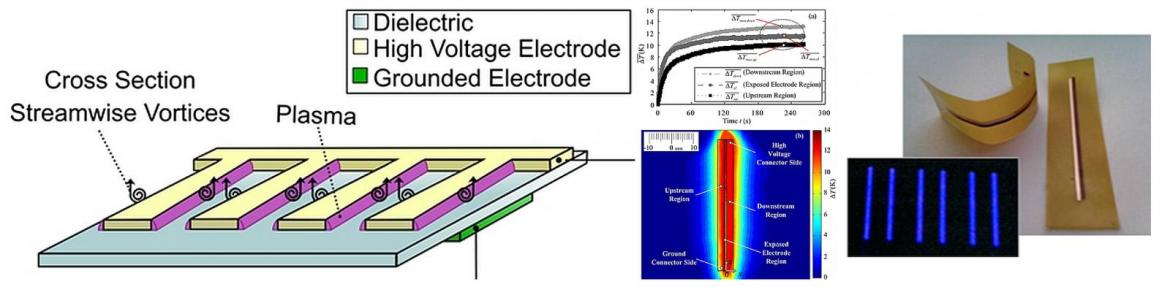
Present research activity is devoted to design, fabrication and functional tests of low cost capacitive pressure sensors coupled with dielectric barrier discharge (DBD) plasma actuators to detect and control the flow separation effect in aeronautics and wind turbine applications. Preventing the flow separation could enhance the performance of propulsion systems and future civil aircrafts by reducing the fuel consumption, the pollutant emissions and the operating costs. For instance, the separation of the boundary layer on the wings, in particular at take-off and landing, leads to large energy losses, increase of the drag forces and decrease of the aircraft lift. The design of the pressure sensor was optimized for applications such as flow separation detection and indirect stall conditions prediction on aircraft wing profiles and engine turbomachinery blades. Finite element method (FEM) simulations were used to obtain information on the deflection and the stress distribution in different shaped floating membranes and on the sensor sensitivity as a function of the pressure load. To this aim a fast detection of boundary layer separation is mandatory for a sustainable and successful application of active flow control devices, as plasma actuators. The fabrication process has been developed on Kapton foil for conformal installation on wing profiles and coupling with capacitive pressure sensors. Experimental tests are performed in cooperation with GE Lab of University of Salento in Italy.
Contact person: Luca Francioso